Training Green Belt Six Sigma
Are you ready for the next step in Lean Six Sigma? Our Green Belt training covers both Lean and Six Sigma principles. This specialised training is ideal for project managers who strive for an integrated approach to continuous improvement.
This intensive training course highlights both Lean and Six Sigma principles and equips you with the tools needed to minimise waste in processes. In addition, the focus is on statistical models to control variations, all within the proven framework of the DMAIC methodology.
What to expect from our Green Belt Lean Six Sigma training?
Our training focuses on motivated and active participation, with no prior preparation required. Specific prior knowledge is not required, although attending Yellow Belt training will be a plus.
During this training we put our emphasis on practical experience with varied, hands-on problem-solving exercises. Theory is applied directly using examples and real project cases, giving participants the opportunity to practice and refine their skills.
In addition to the theory, a practical case takes place within the participant’s own work environment, where the participant is coached and guided by our Master Black Belt.
Lunch is provided on site, including drinks and snacks. After the training, you are welcome to join Perfact’s Friday afternoon drinks if you like.
Learning Objectives Green Belt Lean Six Sigma Training.
By the end of the training you will be able to:
- Understand the basic principles of Lean Six Sigma;
- Learn the Six Sigma principles and understand how to adopt a systematic approach to continuous improvement;
- Understand Six Sigma practice and specific tools to reduce variation using statistical models;
- Expand knowledge in Six Sigma techniques using the DMAIC method;
- Apply DMAIC and common tools to solve daily problems;
- Facilitate the “Problem Solving” process for the identified problem (with coaching).
Perfact Lean Academy
Our Lean Training Program is accredited by the leading accreditation body LCS (Lean Competency System). All components of our training system are aligned with the LCS principles of “Lean Thinking” and are designed to support a systematic approach to continuous improvement. We share our Lean knowledge and thinking in such a way that everyone is able, using a particular method, to create a work environment where continuous improvement is paramount.
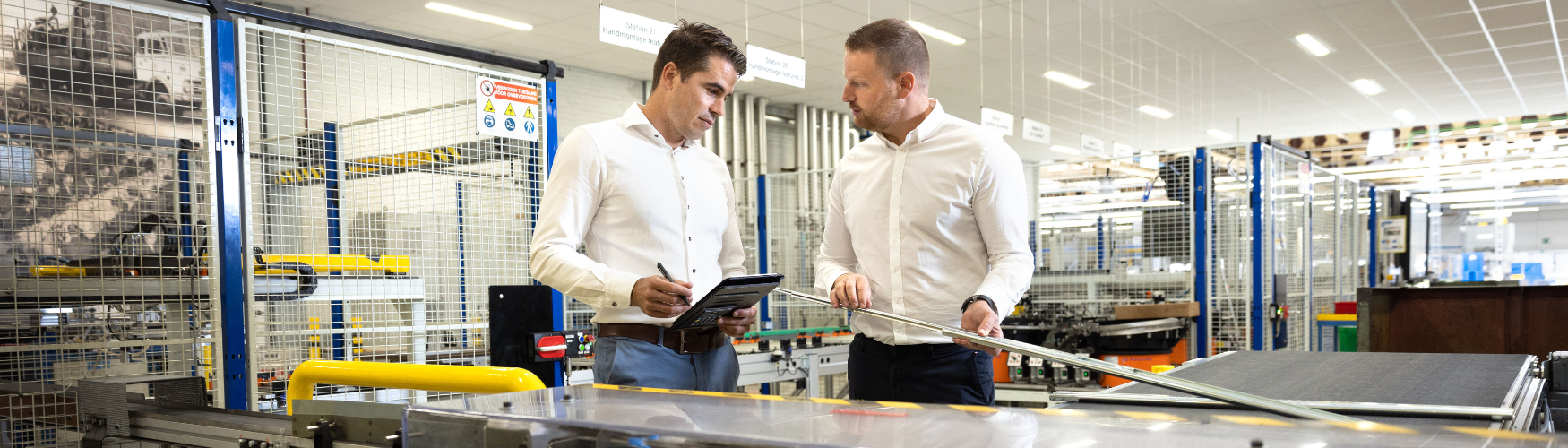
Lean Assessment: the first step to continuous improvement
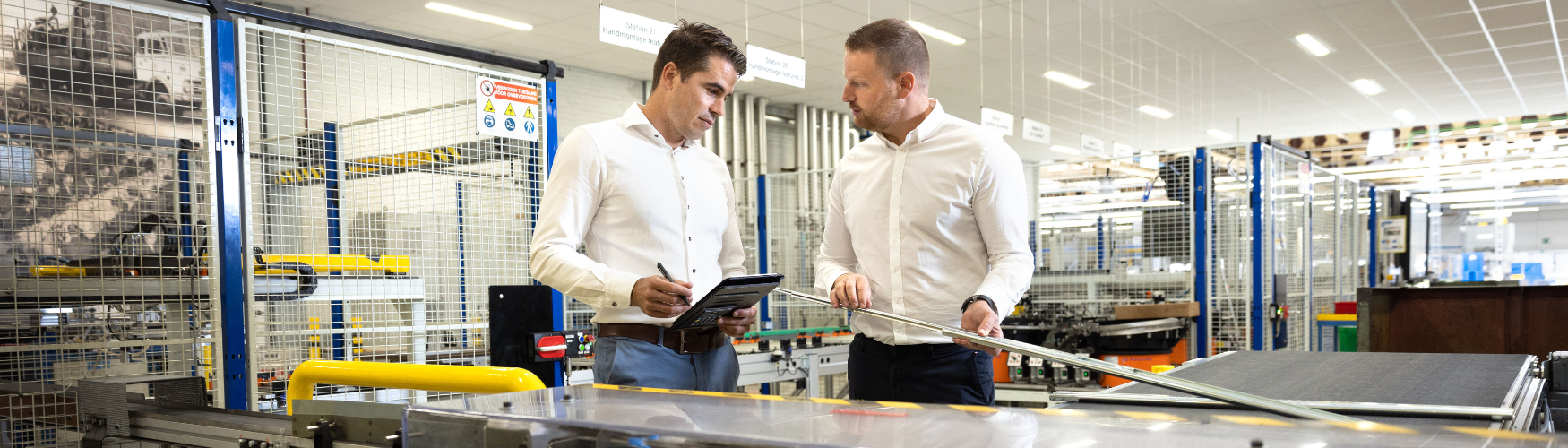
Lean Assessment: the first step to continuous improvement
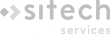

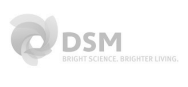

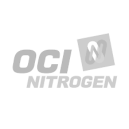

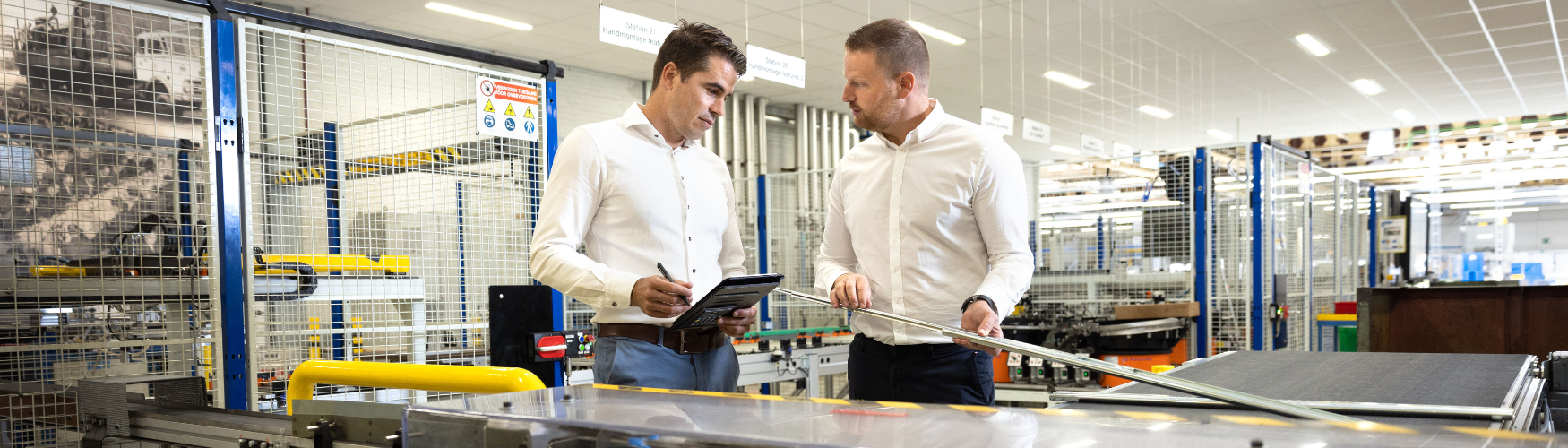
Lean Assessment: the first step to continuous improvement
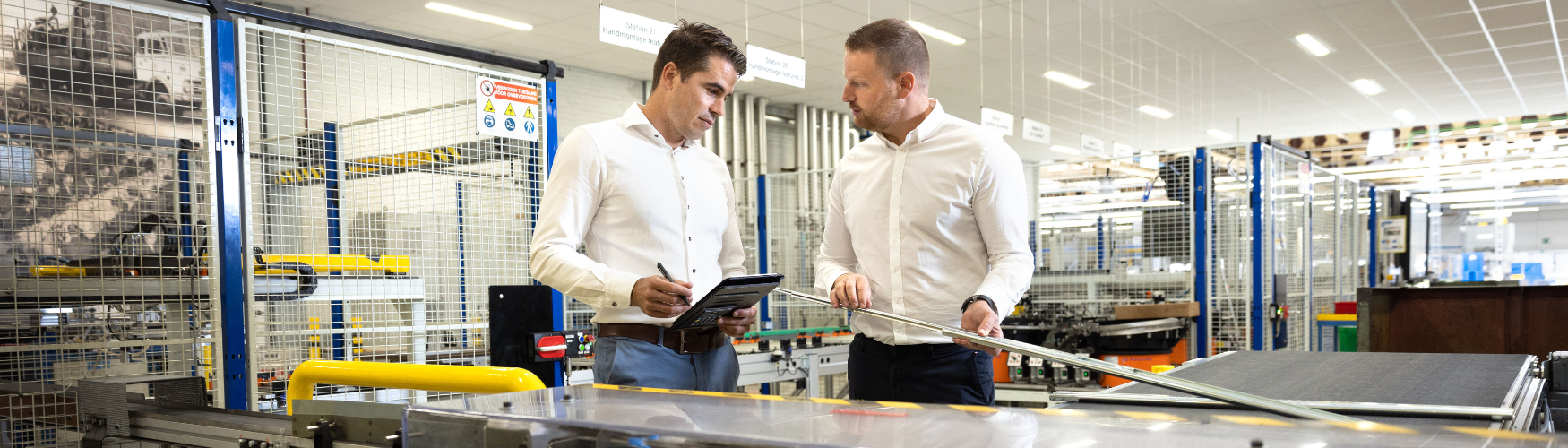
Lean Assessment: the first step to continuous improvement
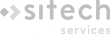

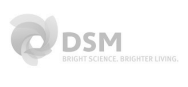

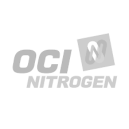
