The Orange Belt Lean Training is specifically designed for all team members involved in improving processes within their organization. This insight adds value in achieving overall organizational goals. The classroom Orange Belt training takes 2 days and there are no other entry requirements you must meet.
Training Lean Orange Belt
Learning Objectives
The Orange Belt Lean training provides an introduction to process management and covers specific Lean topics, giving participants a better understanding of processes and the ability to provide meaningful assistance in meeting overall organisational goals.
During LEAN Orange Belt training, you will be taught techniques that will enable you to lead Lean projects through the key stages of Lean Sigma. It includes a deepening of the Lean Sigma tools and the DMAIC(Define, Measure, Analyze, Improveand Control) phases.
By the end of the training you will be able to:
- Understand the basic principles/fundamentals of Lean Six Sigma
- Have in-depth knowledge of Lean, Six Sigma & DMAIC methodology
- Learn techniques in guiding Lean projects through the key stages of DMAIC
Who can participate in our Lean Orange Belt training?
The training is ideal for any employee who will be involved as a participant in Lean activities and is set to improve an organisation on a daily basis. In addition, you can use this training as excellent preparation for any follow-up training within Lean (such as the Green Belt).
Training Model & Course Duration
The LEAN Orange Belt – Practitioner training is a hands-on classroom training, carried out by a certified Master Black Belt and lasts 2 days.
This course is an accredited LCS-1b level training and requires no prior preparation. To earn the LCS certification, students must pass a theoretical assessment (exam) and complete a practical assessment by performing 1 small improvement project/ A3 as a project owner.
Perfact Lean Academy
Our Lean Training Program is accredited by the leading accreditation institute LCS (Lean Compentency System). All components of our training system are aligned with the LCS principles of “Lean Thinking” and appropriately developed to support a systematic approach to continuous improvement. We are able to share our Lean knowledge and thinking in such a way that everyone is able, by using a particular method, to create a working environment in which continuous improvement is paramount.
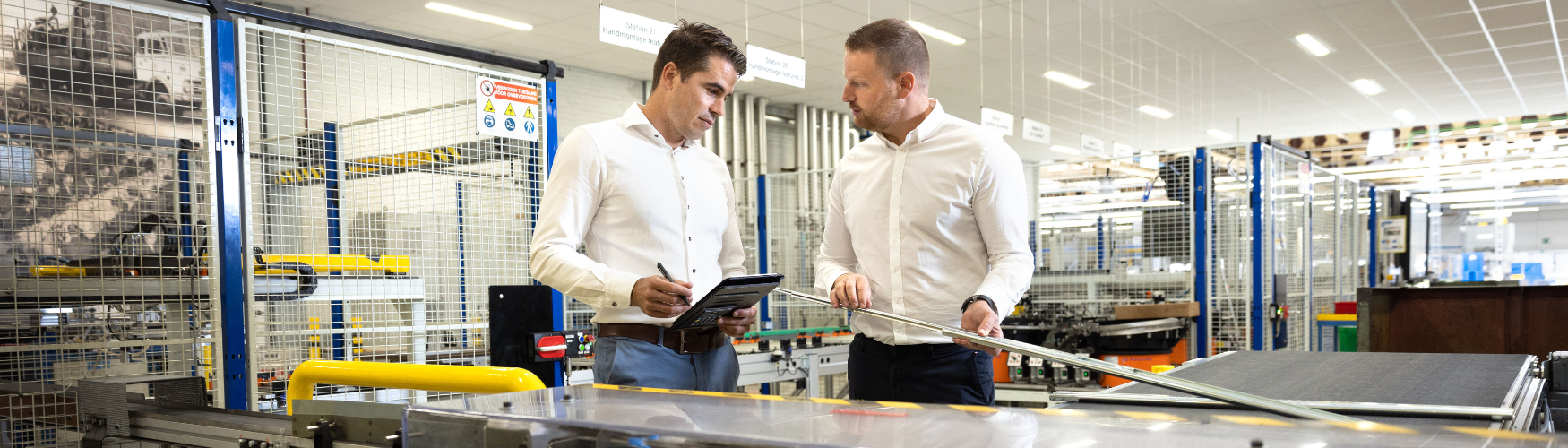
Lean Assessment: the first step to continuous improvement
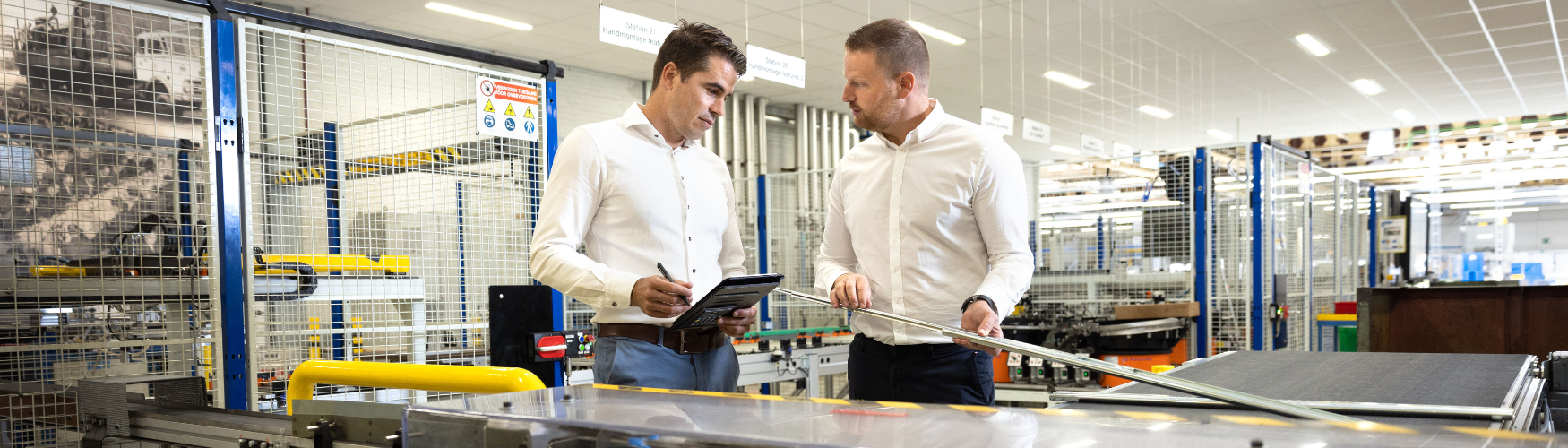
Lean Assessment: the first step to continuous improvement
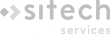

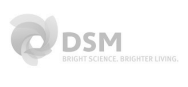

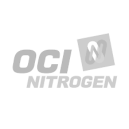
